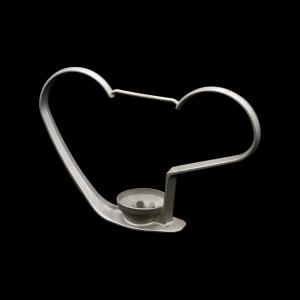
Add to Cart
OEM investment in foundry stainless steel precision castings
What is precision casting?
Precision casting is a lost wax casting process. It is also called investment casting and is widely used in the production of ferrous and non-ferrous metal castings. The lost wax method of precision castings is suitable for producing castings with complex shapes and high dimensional accuracy. Precision castings have excellent surface finish and dimensional accuracy. Its products have a net shape or a near-net shape. Suitable for low-quantity request orders. In addition, precision castings have great freedom in the design and material selection of castings. It allows multiple types of steel or alloy steel to be used for investment. Therefore, in the casting market, precision castings are the highest quality castings.
We are a Chinese precision casting foundry located in Shandong. Through the precision casting process, we can cast nearly 300 alloys. Our metals include stainless steel, tool steel, carbon steel and ductile iron, aluminum, copper, brass and other alloy steels. Precision casting is suitable for complex and detailed parts design, such as impellers. Because it uses the lost wax ceramic shell. The pattern is injection molded in advance. After pouring, it can be finished. If the requirement is more perfect, it can be processed and post-treated.
Precision casting also faces molding and time costs. For each casting production, it needs a mold and a wax pattern. This will require more time and separation costs. Therefore, for low-volume products, this is not economical.
Process | precision Casting, other process can be customized. |
Material | Alloy steels, Carbon Steel , Stainless steel, Malleable iron , Grey iron, Ductile iron Aluminum, Bronze etc. |
Unit Weight | 0.1kg-100kg |
Finish | Plain,Nickel Plating , Chrome Plating or Polishing |
Application | Automotive ,Mining, Railway, Construction equipment,Mining etc |
Quality Control | CMM, Projection Machine, spectrometer, Hardness tester, Tensile tester etc. |
Certificate | ISO 9001:2008 |
Standard | ASTM,DIN,ISO,BS,JIS |
Precision castings have many process steps, so each casting requires more time. Next is the introduction of precision casting process.
Precision casting process
step 1. Mold release
Our engineers will complete the mold design. The mold is purchased from a mold factory.
Step 2. Wax injection
The wax is sprayed by the machine. The wax design of the required casting is produced by injection molding. These processes are called patterns.
Step 3. Assembly tree
The patterns are attached to the central wax stick, called "trees", to form cast clusters or assembly trees.
Step 4. Shell making
The housing is manufactured by immersing the components in a liquid ceramic slurry and then immersing in a bed of extremely fine sand. Up to six layers can be applied in this way. The shell will dry out during each layer of production.
Step 5. Devax
Once the ceramic is dry, it is then heated. The wax will melt away. The melted wax will flow out of the shell.
Step 6. Casting
In the traditional process, the shell is filled with molten metal by gravity pouring. As the metal cools, the parts and gates, gates and pouring cups become solid castings.
Step 7. Knockout
When the metal cools and solidifies, the ceramic shell will be cut off by the vibration or elimination machine.
Step 8. Cut off
Use a high-speed friction saw to cut the part from the central spruce.
Step 9. Grinding
After the casting is cut. Cast parts will be carefully ground.
Step 10, inspection and post-processing.
The inspector will inspect the castings according to the drawings and quality requirements. If there are unqualified parts. Will repair and check again.
Step 11. Finished casting
After the surface treatment operation, the metal casting is the same as the original wax model, ready to be shipped to the customer.
ic systems and grid plates for filter systems.